Gießerei-Industrie = Recycling-Industrie
Wirtschaftslage und Perspektiven
Kennziffern, Strukturen und Abnahme der deutschen Gießerei- Industrie waren Inhalt eines Beitrages in Heft 53 im Januar 2019. Insbesondere die Kapitel „Ausblick“ und „Initiative Guss“ bewirkten einen überraschend intensiven Diskussionsprozess, der deutlich über die Branche der Hersteller und Abnehmer gusseiserner Rohrsysteme hinausging. Doch zunächst sei ein Gesamtblick auf die wirtschaftliche Situation der deutschen Eisen- und Stahlgießereien gestattet.
Geschäftslage der Gießerei-Industrie
Der wirtschaftliche Verlauf des Jahres 2019 entspricht in nahezu allen Kennziffern keinesfalls der erfolgreichen Entwicklung in 2018. Bereits per Juli 2019 sank die Gussproduktion der deutschen Eisen- und Stahlgießereien um fast 9 %. Wesentlich kritischer entwickelte sich jedoch der Auftragseingang mit 17 % unter den Werten des Vorjahreszeitraumes. Damit schwinden natürlich die Auftragspolster wie die sprichwörtliche „Butter in der Sonne“.
Unter Berücksichtigung der Abnehmerstruktur ergibt sich hinsichtlich des Produktionsniveaus der deutschen Eisen- und Stahlgießereien folgendes Bild [1]:
Fahrzeugbau: – 18,9 %
Maschinenbau: – 13,4 %
Sonstige Verwendungszwecke (einschließlich Bauguss): – 1,0 %
Gesamt: – 8,6 %
Leider bestätigt sich damit die bereits in Heft 53 auf Seite 18 abgegebene Marktprognose für 2019 wesentlich deutlicher als vorhergesehen. Die Einordnung der hoch- gerechneten Eisen- und Stahlgussproduktion in die Entwicklung seit 2003 holt die Gießereien dann endgültig auf den Boden der Tatsachen zurück.
1 Mio. t der geschätzten Gießereikapazität von 4,8 Mio. t, hoch gerechnet für Eisen- und Stahlguss, wird im Jahr 2019 nicht benötigt. Das entspricht einer Auslastung der Gießereien von ca. 80 %. Schließlich sei zur Geschäftslage bereits zu diesem Zeitpunkt auf ein schwieriges erstes Halbjahr 2020 hingewiesen. Aus dem exorbitant schlechten Auftragseingang im Verlauf des Jahres 2019 kann leider nur diese Prognose für 2020 aus gegenwärtiger Sicht gegeben werden.
Ursachen und Einordnung
Die Ursachen sind vielfältig und spezifisch für die jeweiligen Abnehmerbereiche. Branchen übergreifend sind es die internationalen Handelsstreitigkeiten, die vor allem den exportorientierten Fahrzeug- und Maschinenbau behindern so- wie die steigenden Unsicherheiten des BREXIT-Prozesses. Spezifisch ist beispielsweise der E-Mobilitätshype, der den deutschen Gießern für Fahrzeugkomponenten nicht nur einen konjunkturellen Abschwung, sondern längst eine strukturelle Krise beschert.
Und insbesondere Betriebe mit dem Produktionsschwerpunkt Guss-Rohrsysteme leiden darüber hinaus an den kritikwürdigen Wirtschaftssanktionen gegen Russland als einen der interessantesten Zukunftsmärkte für die Wasserversorgung. Im Gegenzug gewinnen chinesische Anbieter in dem Maße russische Märkte hinzu, wie sie andererseits mitteleuropäischen Herstellern verloren gehen.
Schließlich wirkt Abnehmerbranchen übergreifend die zunehmende Verschlechterung der wirtschaftlichen Rahmenbedingungen in Deutschland. Eine Aufzählung würde den Umfang des Beitrages sprengen, daher sei nur als eines der signifikantesten Beispiele die Entwicklung der Energieaufwände genannt. Nicht nur die Höhe der Strompreise an sich ist sowohl in Europa als auch weltweit einmalig. Viel stärker rücken Unsicherheiten in der Grundlasterzeugung und in der Energieübertragung einschließlich der damit verbundenen und bisher völlig unklaren, zukünftigen Kosten in den Fokus der industriellen und privaten Verbraucher.
Und wie bereits bei der chemischen Industrie besteht auch bei den Gießereien Klarheit darüber, dass die zweifellos notwendigen Investitionen zur weiteren Absenkung des Ausstoßes von Treibhausgasen den Strombedarf und damit die Stromkosten massiv erhöhen werden [2].
Zusammenfassend ist also festzuhalten, dass sich zwischenzeitlich nahezu alle Abnehmerbranchen in strukturellen Umbrüchen infolge Veränderung verschiedenster branchenspezifischer Rahmenbedingungen befinden.
Für Hersteller von Guss-Rohrsystemen ist diese Situation allerdings nicht ganz neu. Seit Jahrzehnten dominiert in dieser Branche der Wettbewerb der Werkstoffe, insbesondere fokussiert auf Gusseisen gegen Kunststoffe.
Völlig neue Impulse erhält diese Debatte zum einen durch die immer stärker werdenden Erkenntnisse zu den Wirkungen von Kunststoffen auf die Umwelt und den Menschen [3]. Zum anderen dadurch, dass die Gießerei-Industrie im Allgemeinen sowie die Hersteller von Guss-Rohrsystemen im Besonderen das Thema Kreislaufwirtschaft (Circular Economy) und damit den effizienten Umgang mit Ressourcen schon seit längerem abbilden.
Die Herstellung von Guss-Rohrsystemen – Ausgangssituation und Perspektiven
Der Wandel im Herstellungsprozess zum effizienten Umgang mit Ressourcen läuft nach Auffassung des Autors seit Beginn des 21. Jahrhunderts nachdrücklicher als je zu- vor und ist trotz bisher erreichter, sehr beachtlicher Erfolge, längst nicht abgeschlossen (sofern es überhaupt einen Abschluss gibt!). Drei signifikante Beispiele zeigen im Folgenden plakativ die erreichten Arbeitsstände und die noch zu erledigenden Aufgaben.
Erstens, der Schmelzprozess
Letztmalig enthält die Ausgabe des Handbuches „Guss-Rohrsysteme“ von Juli 2011 auf Seite 3/2 ein eigenes Kapitel zum Hochofenprozess. Demnach kann Eisen zur Herstellung von Rohren und Formstücken entweder als Roheisen erster Schmelzung oder als Recyclingwerkstoff aus Stahlschrott, Gussbruch, Gussschrott und Gießereiroheisen erzeugt werden. So- weit der damalige Text, ergänzt durch die Abbildung eines Hochofenabstichs [4].
Der sogenannte Flüssigverbundbetrieb als direkte Beschickung von flüssigem Roheisen aus den Hochöfen in die nachgeschalteten Induktionsrinnenöfen der Rohrgießereien war über Jahrzehnte charakteristisch für die Produktion von Gussrohren, teilweise auch von Formstücken aus Gusseisen. Flüssiges Roheisen und schließlich die Rohrkörper entstanden nahezu ausschließlich aus der Reduktion der weltweit begrenzt vorhandenen Ressource Eisenerz mit Hilfe von Koks und Kalkstein im Hochofenprozess.
Den fundamentalen Wandel dokumentiert das gleiche Handbuch mit Ausgabe Oktober 2015 im einführenden Satz auf Seite 3/4. Üblicherweise erschmelzen die Gießereien nun ihr Eisen im Kupolofen- oder Elektroschmelzbetrieb aus Recyclingmaterial und Roheisen [5]. Ins- besondere beim Kupolofenbetrieb werden heute zu 100 % Schrotte mit verschiedenen Klassifizierungen eingesetzt. Im Umkehrschluss besteht demnach der Gussrohrkörper ausschließlich aus recycelten Materialien. Die Verhüttung von Eisenerzen entfällt komplett.
So weit, so gut, wenn da nicht die zunehmende CO2-Debatte wäre. Unter Berücksichtigung, dass bei der Verbrennung von einem Kilogramm Kohlenstoff 1,87 m³ CO2 entstehen und der hiesige Koks ca. 91 % Kohlenstoff enthält, ergeben sich bei der Verbrennung von einem Kilogramm Schmelzkoks 1,7 m³ bzw. 3,36 kg CO2. Nicht richtig ist die Annahme, dass bei einer Satzkoksmenge von 130 kg der CO2-Ausstoß 437 kg pro Tonne Flüssigeisen beträgt. Ein Großteil des im Koks enthaltenen Kohlenstoffs reichert im Kupolofenbetrieb infolge sehr komplexer Reaktionen den C-Gehalt der Schmelze bis hin zum gewünschten Wert an. Ungeachtet dessen entsteht jedoch in Abhängigkeit von Bau- und Betriebsart der Kupolofenschmelzanlage CO2.
Vordergründig zu behandelnde Zielstellung für dieses Schmelzverfahren ist demnach die Erreichung einer effizienteren Verbrennung. Ein spezielles Verfahren zur Sauerstoffeindüsung wird zukünftig den Schmelzkoksverbrauch signifikant senken und damit zu einem deutlich geringeren CO2-Ausstoß führen.
Ein zunehmend eingesetztes Schmelzaggregat in Eisengießereien ist der Induktionstiegelofen. Das Schema in der Abbildung zeigt den grundsätzlichen Aufbau eines Elektroschmelzbetriebes mit drei Induktionstiegelöfen der Bauart ABP [6].
Die feuerfest ausgekleideten, zylindrischen Gefäße sind mit Wechselstrom durchflossenen Spulen umgeben, wodurch im metallischen Einsatz ein Sekundärstrom induziert wird. Bei optimalen Flüssigeisenabnahmebedingungen stellt sich ein Energieverbrauch von 580 bis 600 Kwh/t Flüssigeisen bei ca. 1.480 °C Abstichtemperatur ein. Wird der benötigte Schmelzstrom aus erneuerbaren Energien bezogen, ergibt sich tatsächlich eine hervorragende Umweltbilanz und Energieressourceneffizienz. Der ursprünglich auf mittelständische Gießereien mit durchschnittlich 18.000 t Gussproduktion bzw. 27.000 bis 30.000 t Flüssigeisen begrenzte Einsatz ist ebenfalls Geschichte. ABP Dortmund errichtet mittlerweile weltweit Schmelzanlagen für mehr als 80.000 t Flüssigeisen.
Allerdings sind auch bei Elektroschmelzbetrieben Hausaufgaben zu erledigen, wenn auch abweichend zu denen des Kupolofens. Der metallische Einsatz für Induktionstiegelöfen enthält nicht nur Stahl- schrotte, sondern erfordert infolge des fehlenden Kohlenstoffträgers sowie des veränderten Keimhaushalts einen gewissen Anteil Roh- eisen. Er schwankt in Abhängigkeit von Gussteilstruktur, Gussherstellungsverfahren sowie Gussqualität selbst praktisch zwischen 5 und 30 % im kalten Satz.
Zusammenfassend bleibt nach gegenwärtigem Wissensstand festzuhalten, dass eine weitere Senkung von Roheisenanteilen in der Gattierung von Induktionstiegelöfen realistischer im Vergleich zu einer deutlichen Absenkung des CO2-Ausstoßes von Kupolöfen erscheint. Daraus schlussfolgernd stellt schon heute der Elektroschmelzbetrieb mit Mittelfrequenz-Induktionstiegelöfen selbst für Rohrgießereien unter Umweltaspekten eine interessante Alternative dar.
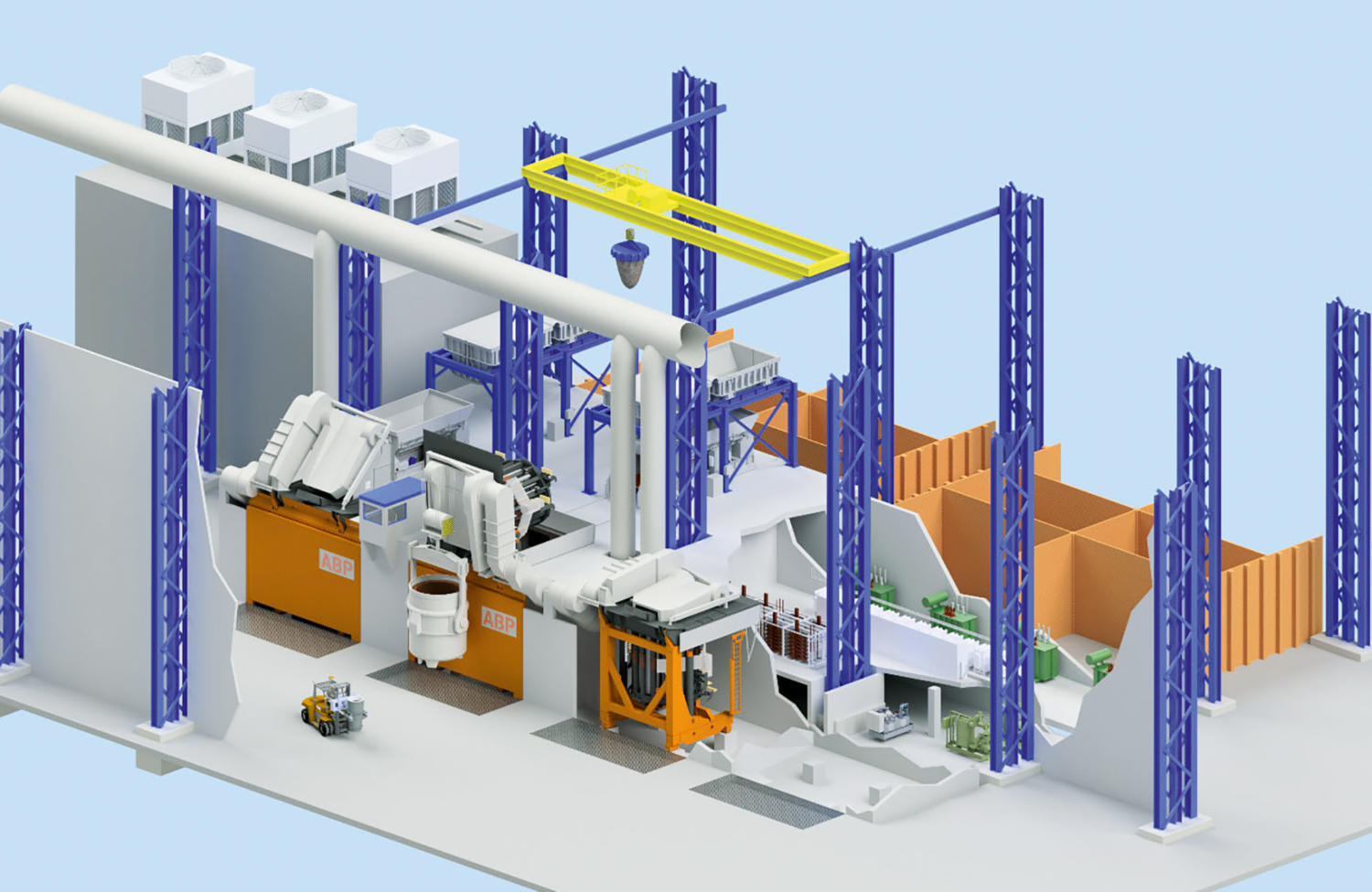
Elektroschmelzbetrieb mit drei Induktionstiegelöfen.
Zweitens, der Strahlprozess
Eher unscheinbar und daher oft stiefmütterlich behandelt, ist der Strahlprozess in den Formstück- und Armaturengießereien. Sofern die Gießereien nachgeschaltete Beschichtungsanlagen betreiben, wird das gießereiübliche Rohgussstrahlen zur Beseitigung anhaftender Sand- und Kernreste durch eine spezielle Oberflächenbehandlung mittels Strahlen ergänzt. Ziel ist die Erreichung eines größtmöglichen Reinheitsgrades, auch Oberflächenvorbereitungsgrad genannt, von mindestens Sa 2 1/2, unmittelbar vor dem Beschichtungsprozess. Die Strahlmaschinen enthalten in der Regel Stahlguss-Strahlmittel mit runder Körnung und Korngrößen von 1,0 bis 1,6 mm. Spezielle Strahlprozesse erfordern eine anteilige Zumischung kantiger Strahlmittel.
Weniger bekannt und daher vernachlässigt ist der hohe Energieverbrauch durch unkontrollierten Strahlmaschinenbetrieb. Der führende Strahlmittelhersteller Würth in Bad Friedrichshall hat sich nun typenunabhängig dieser Problematik angenommen und beschäftigt sich seit geraumer Zeit mit entsprechenden Energieeffizienzprogrammen. Den bisherigen Arbeitsstand zeigt die Abbildung „Strahlprozessüberwachung“ [7].
Die zielgerichtete Sensor-Überwachung und gleichzeitige Datenaufzeichnung verschiedenster Strahlmaschinenfunktionen führt zu einer höchstmöglichen Prozesstransparenz. Mit dem Projekt AP-Con – Abrasive Process Control – erschließen sich Energieeinsparpotenziale von > 20 %.
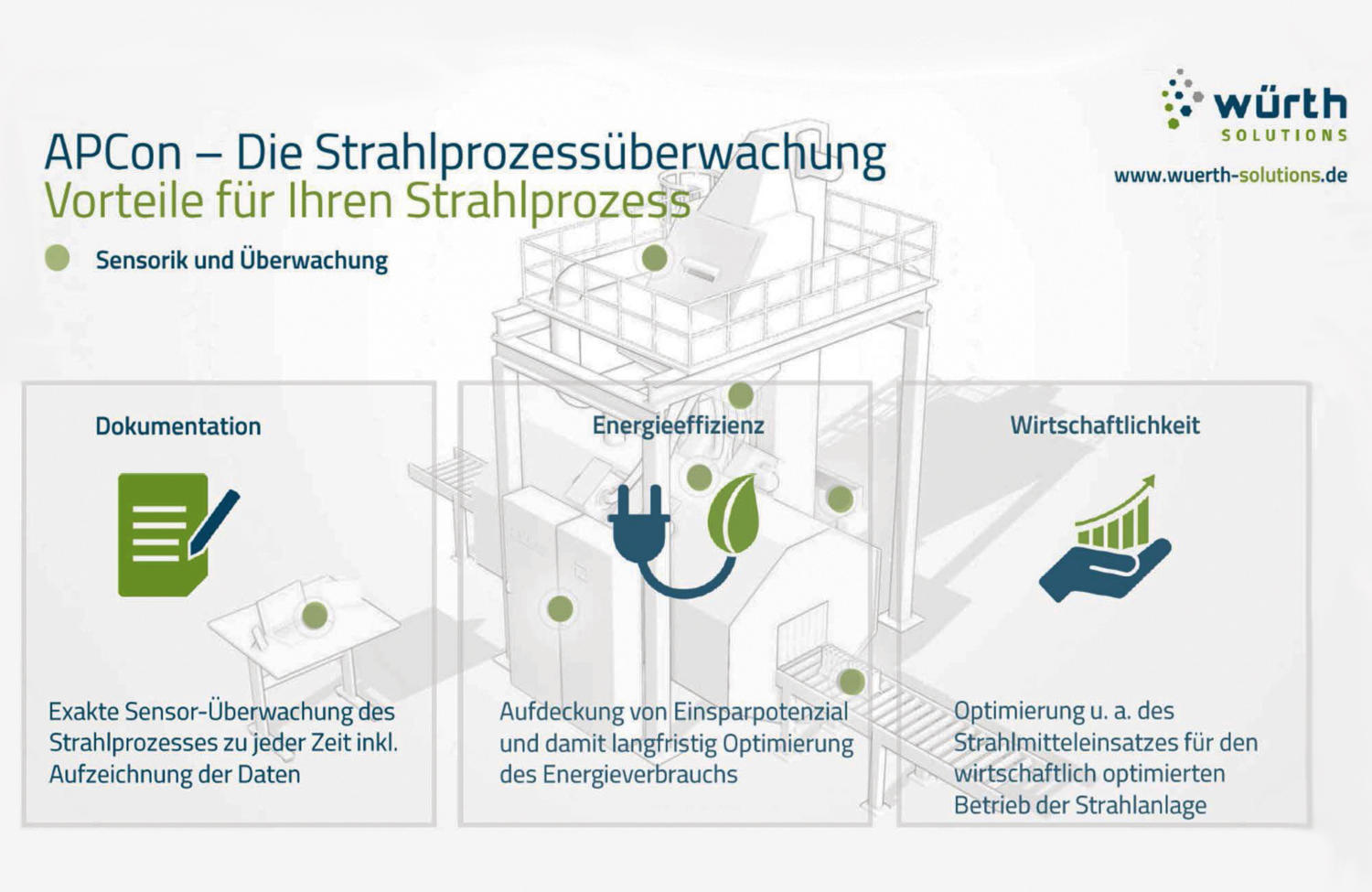
Strahlprozessüberwachung.
Drittens, der Regenerierungsprozess Bentonit gebundener Mischaltsande
Die Gießer unterscheiden hinsichtlich des Formverfahrens zunächst zwei grundlegende Möglichkeiten:
-
Dauerformen, u. a. zur Herstellung von Gussrohren im Schleudergussverfahren mit Hilfe metallischer Kokillen sowie
-
verlorene Formen, d. h. Verfahren mit Formen zum einmaligen Gebrauch.
Formstücke sowie Gussteile für Hydranten und Armaturen werden nahezu ausschließlich mit verlorenen Formen und entsprechenden Kernen zur Hohlraum- bzw. Konturenbildung hergestellt. Während Gussteile für Guss-Rohrsysteme größerer Nennweiten in chemisch gebundenen Formstoffen handgeformt werden, erfolgt die Herstellung kleinerer Nennweiten, i.d.R. bis DN 400, auf Formanlagen mit Bentonit gebundenen Grünsanden im Sandkreislauf. Insbesondere durch den Zulauf von Kernsanden, als gelbe Linie in der Abbildung dargestellt, kommt es zum Anfall von Überlaufsanden [8]. Dieses Gemisch aus Bentonit gebundenem Formstoff und Kernresten, teilweise sogar aus verschiedenartigen Kernherstellungsverfahren, wird als Mischaltsand oder Gießereialtsand bezeichnet.
Die Regenerierung von Mischaltsanden mit der Zielstellung des Wiedereinsatzes der Quarzsande in der Kernmacherei bei gleichzeitiger Wiederverwendung der anfallenden Bentonit- und Kohlenstoffkomponenten im Sandkreislauf, er- weist sich infolge fehlender komplexer Regenerierungsverfahren als gegenwärtig nicht durchführbar. Dabei sind die jährlich anfallenden Altsandmengen nicht unerheblich. Allein die sächsischen Eisen- und Stahlgießereien deponieren jährlich ca. 220.000 t bei einer Gussproduktion von ca. 320.000 t.
Besonders hoch ist der Gießereialtsandanfall bei der Herstellung von Formstücken sowie Gussteilen für Hydranten und Armaturen. Geringe Gusswanddicken umschließen i.d.R. großvolumige Kerne und führen konfigurations- und prozessbedingt zu schlechten Guss-Sand- Verhältnissen. Unabhängig von der kritischen Stoffbilanz selbst, ergibt sich aus den knapper werdenden Deponieräumen in Deutschland ein weiterer und dramatisch zu- nehmender Zwang nach einer Schließung des Gießereisandkreislaufes.
Aber auch dazu wird gehandelt. In Absprache mit den am stärksten betroffenen sächsischen Eisen- und Stahlgießereien sowie dem Landes- verband Ost des Bundesverbandes der Deutschen Gießerei-Industrie, starteten das Gießerei-Institut und das Institut für Aufbereitungsmaschinen der Technischen Universität Bergakademie Freiberg ein F&E-Projekt. Der wissenschaftliche Anspruch des Projektes besteht in der Entwicklung einer geeigneten Recyclingtechnologie für Überlaufsande mit schwankenden Kernsandanteilen, der gesamtheitlichen technologischen und wirtschaftlichen Betrachtung des Regenerierens der Überlaufsande und des Wiedereinsatzes des erzeugten Regeneratquarzsandes, einschließlich der erzeugten bentonit- und kohlenstoffhaltigen Komponenten mit energetischer Erfassung der einzelnen Vorgänge. Starttermin ist das erste Quartal 2020.
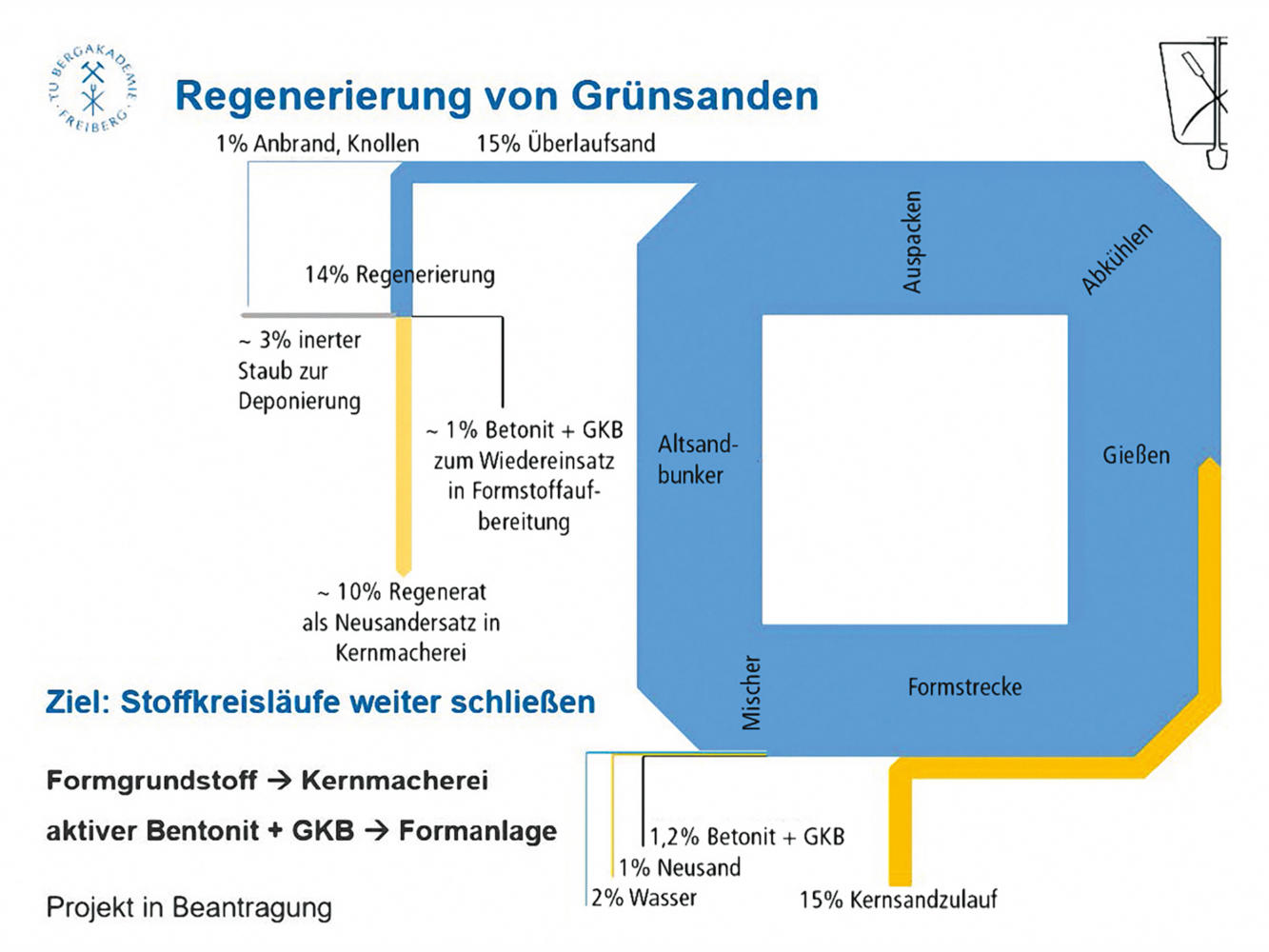
Grobdarstellung des Sandkreislaufes von Formanlagen.
Zusammenfassung
Hersteller von Guss-Rohrsystemen haben bereits heute enorme Fortschritte gemacht, den CO2-Ausstoß in den Schmelzprozessen zu reduzieren sowie Stoffkreisläufe zu schließen.
Anhand von drei Beispielen wird plakativ gezeigt, dass diese Prozesse bei weitem noch nicht beendet sind, sondern vielversprechende Lösungen im kommenden Jahrzehnt aus der Branche zu erwarten sind. Alle eingeleiteten Schritte zur Reduzierung des CO2-Ausstoßes sowie zur Schließung von Stoffkreisläufen verfolgen das Ziel, den in der EADIPS FGR vereinten europäischen Produzenten von duktilen Guss-Rohrsystemen eine globale Vorbildrolle im Umgang mit Ressourcen zu attestieren und völlig neue Entscheidungsstandards bei der Auswahl von Rohrsystemen für Netzbetreiber und andere Anwender zu schaffen.
Danksagung
Ein herzlicher Dank geht an die unterstützenden Unternehmen der „Initiative Guss“, insbesondere an Herrn Dr.-Ing. Marco Rische, ABP INDUCTION, Dortmund, sowie an die Herren Joachim Vianden und Timo Winkler, Eisenwerke Würth, Bad Friedrichshall.
Schließlich sei der konstruktiven Mitwirkung des Gießerei-Instituts der TU Bergakademie Freiberg, vertreten durch die Herren Prof. Dr.-Ing. Gotthard Wolf und Dr.-Ing. Marco Weider, gleichermaßen gedankt.
Autor:
Mario Mackowiak, Keulahütte GmbH