1.900 m duktile Gussrohre eingebaut
Berstlining-Verfahren
Der Zweckverband Wasserversorgung Stadt und Kreis Offenbach (ZWO) versorgt insgesamt 14 Städte und Gemeinden vollständig bzw. teilweise mit Wasser aus sechs eigenen Wasserwerken. Zur Wasserverteilung betreibt der Zweckverband Fernwasserleitungen. Wegen zahlreicher Schäden an einem Teilstück einer Fernwasserleitungen mit Rohren DN 200 aus Asbestzement wurde der Teilabschnitt zwischen Mainhausen und Zellhausen erneuert. Zum Einsatz kamen duktile Gussrohre DN 200 der Duktus (Wetzlar) GmbH & Co. KG mit Zementmörtel-Umhüllung nach EN 15542 und längskraftschlüssigen Muffen-Verbindungen.
Die Leitung liegt in einem Landschaftsschutzgebiet. Deswegen wurde ein Großteil der Leitung in geschlossener Bauweise mit dem Berstlining-Verfahren eingebaut. Zudem ließen sich dadurch ca. 50 % der Kosten im Vergleich zur offenen Bauweise einsparen. Beim grabenlosen Rohreinbau wird der Außenschutz duktiler Gussrohre vielfältigen äußeren mechanischen Belastungen ausgesetzt. Um hier Beschädigungen zu vermeiden, empfiehlt sich der Einsatz von mechanisch hochbelastbaren Umhüllungen. Dies gilt im besonderen Maße für Rohre die mit dem Verfahren des Berstlinings eingebaut werden, da die geborstenen Rohrstücke des Altrohres im Boden verbleiben und mit dem Rohr während des Einzugsvorgangs in Kontakt treten können. Die hier eingesetzte Zementmörtel-Umhüllung (ZM-U) schützt die Rohre in idealer Weise vor mechanischen Beschädigungen.
Insgesamt wurde eine Strecke von ca. 2.000 m erneuert, davon 1.900 m im Berstlining-Verfahren. Der längste an einem Stück erneuerte Rohrstrang bestand aus 28 Rohren und hatte eine Länge von 168 m. Die von der Firma Diringer & Scheidel Bauunternehmung GmbH & Co. KG hierfür eingesetzte Maschineneinheit hatte eine maximale Zugkraft von 80 t.
Auch wenn der Einsatz des Berstlinings nach DVGW-Merkblatt GW 323 seit langen erprobt ist und vielfach beschrieben wurde, ließen es sich Fachleute nicht nehmen, die Arbeitsschritte für den Einbau und den Einzug von längskraftschlüssigen duktilen Gussrohren vor Ort erklären zu lassen.
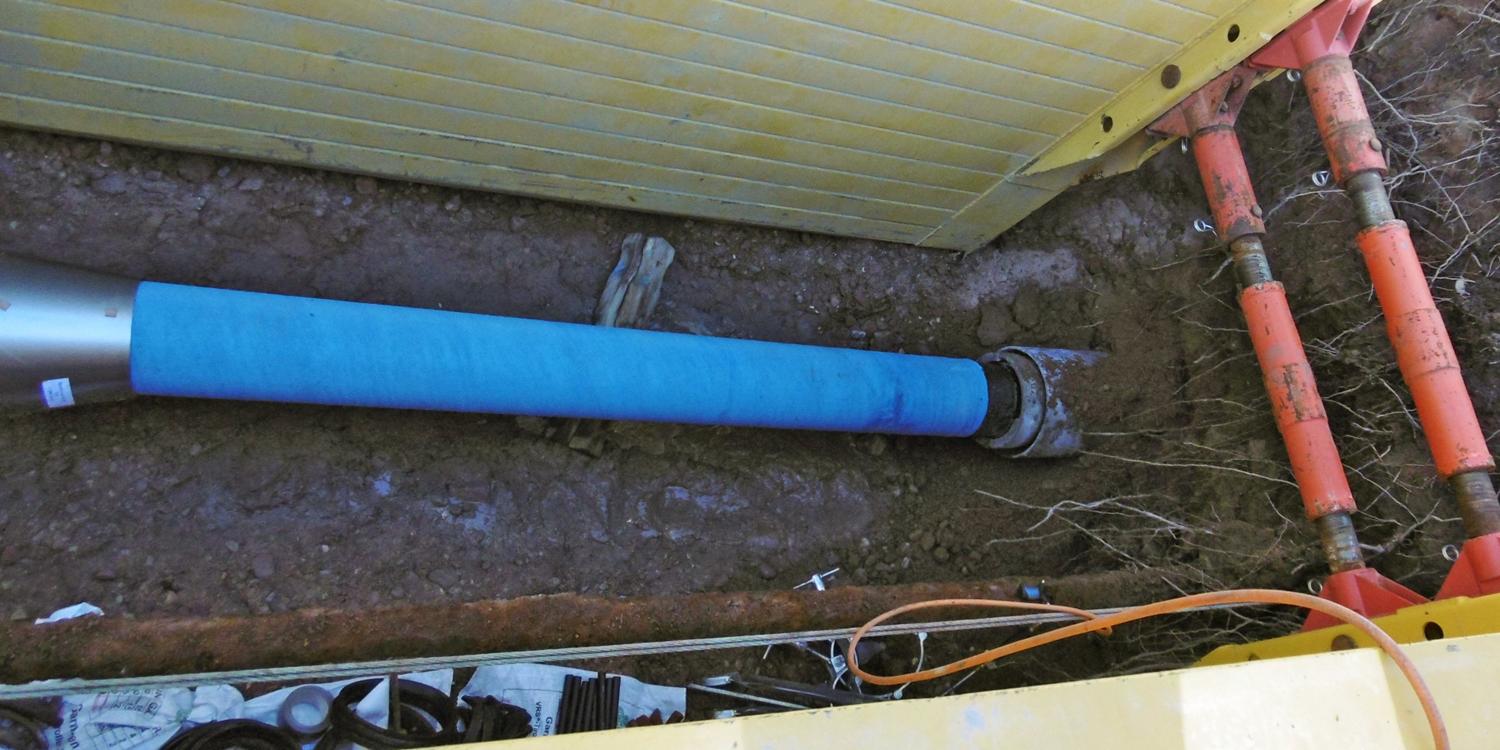
Berstkopf mit angeschlossenem duktilen Gussrohr
DN 200 während des Einzugvorgangs.
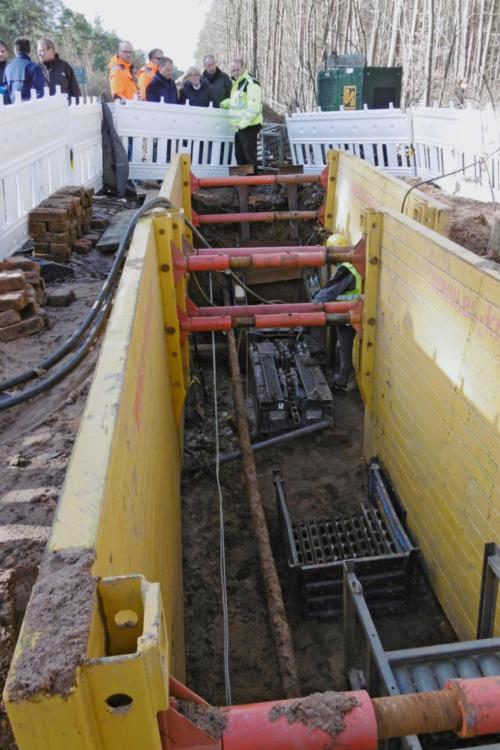
Maschineneinheit mit Zuggestänge in einer
Zielbaugrube
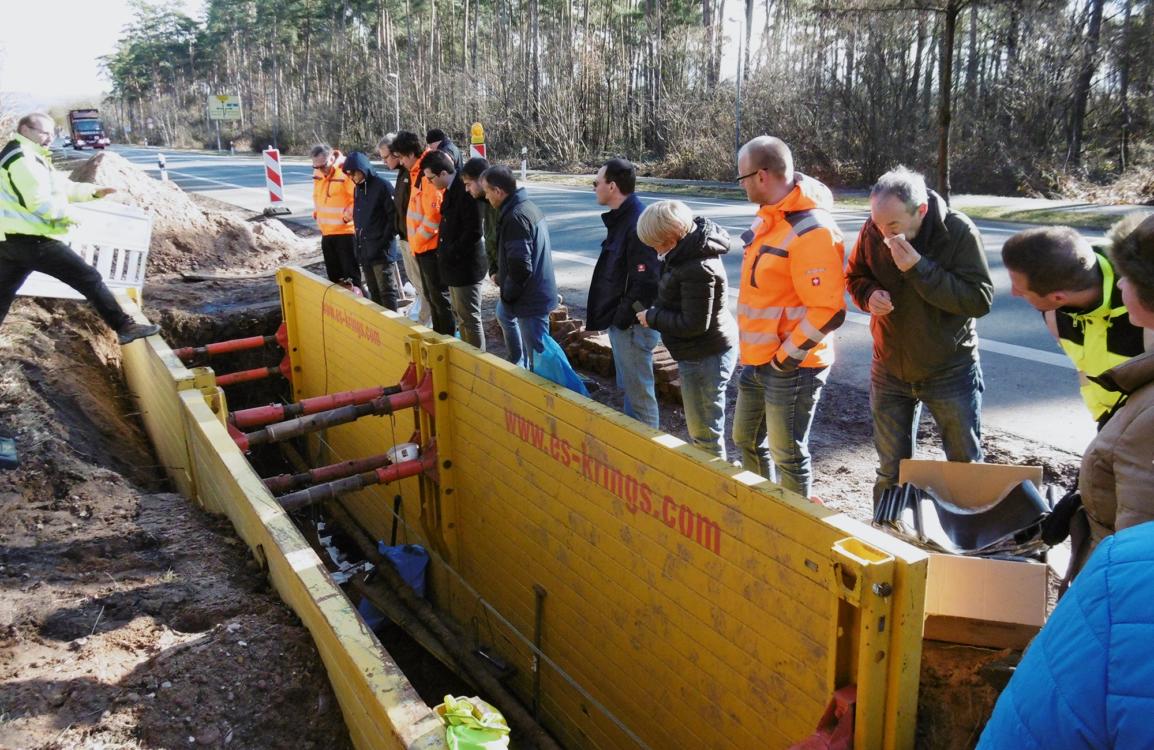
Einem interessierten Fachpublikum wird der Einbau von längskraftschlüssigen duktilen Gussrohren und das Berstverfahren an der Baugrube erklärt.